CONWIP and Kanban
:
- CONWIP
(CONstant work in process) are pull-oriented
production control systems. Such systems can be classified as pull
and push systems (Spearman et al. 1990). In a push system, the
production order is scheduled and the material is pushed into the
production line. In a pull system, the start of each product
assembly process is triggered by the completion of another at the
end of production line. This pull-variant is known for its ease of
implementation.
- CONWIP is a kind of single-stage
kanban system and is also a hybrid push-pull system. While Kanban
systems maintain tighter control of system WIP through the
individual cards at each workstation, CONWIP systems are easier to
implement and adjust, since only one set of system cards is used to
manage system WIP. CONWIP uses cards to control the number of WIPs.
For example, no part is allowed to enter the system without a card
(authority).
- After a finished part is completed
at the last workstation, a card is transferred to the first
workstation and a new part is pushed into the sequential process
route. In their paper, Spearman et al. (1990) used a simulation to
make a comparison among the CONWIP, kanban and push systems, and
found that CONWIP systems can achieve a lower WIP level than kanban
systems.
The Kanban System
:
Kanban is both a type of card and a
control system in manufacturing named after the cards. Both were
developed by Toyota in Japan. There are a limited number of
cards, with each card representing a certain part type and a
certain quantity (at least one). In the picture below, we
have cards for green squares, red diamonds, and blue hexagons. The
kanban can be attached to a part or be separate. Every part
must have a kanban attached with it.

- Assume you have blue hexagons in
stock, each with a card attached. If someone takes out a blue
hexagon, the card is removed from the part and goes back for
reproduction. A card without a part arriving back at the beginning
of the loop is an order to reproduce this part. Hence the card
eventually comes back to storage again with a newly produced
part.
- This is a kanban system in its
simplest form. Of course, there are numerous additional details
like how many cards to use, various prioritizing and grouping
options of the cards for reproduction, and detailed usages of FiFo
lines and supermarkets. For detail, see my numerous posts about
kanban.
The CONWIP System
:
The CONWIP (Constant Work In
Progress) system is very similar to a kanban system, except
that the CONWIP card is not associated with a certain part type,
but only with a certain quantity (also at least one). The
illustration below is comparable to the illustration above except
it represents a CONWIP system.
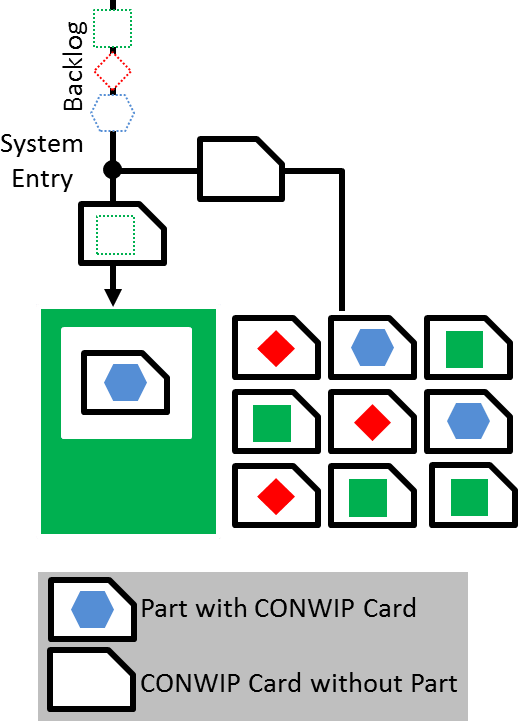
- Completed parts all have a CONWIP
card attached. If the part leaves the system (e.g., it is sold,
used downstream, etc.), the card returns back to the beginning of
the loop. Remember, the card is now not associated with a part
type, only a constant quantity. On its way to the beginning of the
loop, it meets the backlog. The backlog is a list of part types and
quantities that need to be produced. The first part in the backlog
is the most urgent one. If a CONWIP card comes back from the
finished goods inventory, the next part type in line is assigned to
the returning card. The card is hence a signal that capacity is
available, and the backlog defines what to do with the capacity.
The merging of the blank card with the part type is called the
system entry. This part then gets reproduced and eventually makes
its way back to the finished goods of the loop.
- Hence a CONWIP card is like a
kanban card, except the part type gets assigned only on its way
back when it meets the most urgent demand in the backlog.
(2)COMPARISON OF CONWIP AND
Kanban :
Number of Variants :
- Kanban works well with
high-quantity low-variety parts. Since every card has a part number
permanently associated with the card, the cards always replenish
this part number. Of course, this works only if there is a
continuous demand for this particular part number. A good example
of this would be any made-to-stock parts that will be sold in
larger quantities.
- CONWIP, on the other hand, has no
part number assigned by default to the CONWIP card. Hence, any part
number can be assigned (temporarily) to the CONWIP part, even if
the part is produced only once. Therefore, CONWIP is well suited
for made-to-order parts. However, for made-to-stock production, you
need a good production sequence or you may end up in hot water with
CONWIP.
Hybrid System with Kanban Is Quite Possible
:
(3) Overall, I like the CONWIP
system. It seems to be quite useful, especially for made-to-order
products. I can also imagine it to be quite suitable as a hybrid in
combination with kanban. This concludes my four-post series on
CONWIP. I hope this was insightful for you. It definitely was for
me, as I am always learning new things by blogging about them