Railway sleepers
- They are the components on which the rails are arranged with a
proper gauge. (such as broad gauge, narrow-gauge, etc..)
- These sleepers generally rest on the ballast. The load from
rails when the train passes is taken by these sleepers and is
distributed to the ballast.
- They are also known as ties in some regions.
Characteristics of Ideal Railway Sleepers
- Initial cost and maintenance cost should be low
- They should resist weathering, corrosion, decay and other
deterioration
- They should bear the wheel load efficiently and
satisfactorily
- They should maintain the correct gauge
- They should absorb shocks or vibrations due to moving
vehicles
- It should distribute the load properly and uniformly over the
ballast
- Fastenings of rail with sleepers should be strong and
simple
- They should not break while packing of ballast
- Weight should not be low or high
Classification of Railway Sleepers
Based on the materials used, railway
sleepers are classified into the following types.
- Wooden sleepers
- Concrete sleepers
- Mono-bloc concrete sleeper
- Twin-bloc concrete sleeper
- Steel sleepers
- Cast iron sleepers
- Composite sleepers
Wooden Sleepers
- These are sleepers made of wood.
- These are commonly 254mm wide by 127mm thick in cross-section
by 2600 mm long.
- The sleepers are first seasoned (drying for up to 12 months so
that to remove the juice/sap) and treated with preservatives.
Creosote is an oil generally used/ sprayed on the surface.
- Wooden sleepers are used since olden days.
- These are still widely using in some western countries.
- Either hardwood or softwood can be used to make wooden
sleepers. However, hardwood sleepers made of oak, jarrah, teakwood
are more famous.
Two types of timber sleepers
are
-
Switch Ties:
The primary use for switch ties is to transfer load (as from the
name) and are made of hardwood. This type is preferably used in
bridge approaches, heavily traveled, railway crossovers, and
transition ties.
-
Softwood Ties:
softwood timber is more rot (decay)
resistant than hardwood, but does not offer resistance to spike
hole enlargement, gauge spreading, also are not as effective in
transmitting the load to the ballast section as the hardwood
tie.
Softwood ties and hardwood ties should
not be mixed on the main track. Softwood ties are typically used in
open deck bridges.
.
Advantages of Wooden
Sleepers
- Wood sleepers are cheaper than others and easy to
manufacture.
- They are light in weight so, they can be easily transported and
handled while installing.
- Fasteners can be easily installed to wooden sleepers.
They are good insulators so, rails are well protected.
- Any type of gauge can be maintained by wooden sleepers.
- They are suitable for all types of rail sections.
- They are well suitable for tracks in coastal areas.
Disadvantages of Wooden
Sleepers
- They are easily liable to attack by vermin and weather
- They are susceptible to fire
- It is difficult to maintain gauge in case of wooden
sleepers
- Scrap value is negligible
- Their useful life is short about 12 to 15 years.
Steel Sleepers
- Steel sleepers are more often used
because of stronger than wood and economical than concrete.
- They also have a good life span.
- They are molded in trough shape and
placed on ballast in inversed trough shape.
- They are also used in heavy curvature
prone to gauge widening.
- This type of steel ties can cause the
problem to the signals control system.
In the design of Steel sleeper, the
following are considered:
- It should maintain perfect gauge
- Can fix the rail and there should be no movement
longitudinally
- Should have sufficient effective area to transfer load from
rail to ballast.
- The metal of sleepers should be strong enough to resist
bending
- The design life should be 35 years

Advantages of Steel
Sleepers
- They are light in weight so, easy to transport, to place and to
install.
- They are recyclable hence possess good scrap value.
- The life span of steel sleepers is more and is about 30
years.
- They are good resistant to fire.
- They have good resistance against creep
- They cannot be attacked by vermin etc.
- They are well suitable for tracks of high speeds and larger
loads.
- They hold the rail strongly and connecting rail to the sleeper
is also simple.
Dis-advantages of Steel
Sleepers
- Steel can be affected by chemicals easily.
- Steel sleepers require high maintenance.
- They are not suitable for all types of ballast which are
provided as a bed for sleepers.
- If derailment happens, they damaged very badly and not suitable
for reuse.
- These are not suitable for all types of rail sections and
gauges.
Concrete Sleepers
- Concrete sleepers are manufactured by concrete with internal
reinforcement.
- Concrete sleepers used in many countries due to their high
stability and small maintenance.
- These are more suitable for high-speed rails.
- Most of the concrete sleepers are made from pre-stressed
concrete in which internal tension is induced into the sleeper
before casting. Hence, the sleeper withstands well against high
external pressure.
- They have a design life of up to 40 years.
- They can easily be molded into the required/design shape to
withstand stresses induced by fast and heavy traffic.
- The added weight helps the rail to resist the forces produced
due to thermal expansion and which can buckle the track. The weight
of concrete sleepers is about 2.5 to 3 times the wooden
sleepers.
Advantages of
Concrete Sleepers
- Concrete sleepers are heavier than all other types hence, they
give good stability to the rails.
- They have a long life span so, economically preferable.
- They have good Fire resistance.
- Corrosion does not occur in concrete sleepers.
- Vermin attack, decay, etc. do not occur. Hence, they are
suitable for all types of soil and moisture conditions.
- Bucking strength is more.
- Concrete is a good insulator so, this type of sleeper is more
suitable for circuited tracks.
- Concrete sleepers hold the track strongly and maintain
gauge.
Disadvantages of Concrete
Sleepers
- Because of heavyweight, handling is difficult.
- For tracks on bridges and at crossings, concrete sleepers are
not suitable.
- Damage may occur while transporting.
Concrete sleepers are of two
types:
- Mono-bloc concrete sleeper
- Twin-bloc concrete sleeper
Mono-bloc concrete sleeper
- These are the
development of sleepers into prestressed sleepers that took place
about the same time as the development of flat bottomed rail and
direct fastenings.
- It is first in the UK
prestressed concrete sleeper manufactured by the pretension method.
Variations of this standard sleeper are available with extra holes
for supporting conductor rail insulators and with shallower depth
where these conditions apply. In this method, the prestressing
tendons are tensioned prior to the concrete being placed and are
only released once the concrete has reached sufficient compressive
strength to resist the induced forces thus applied. This method is
also sometimes referred to as the 'Long Line' system, as sleepers
are cast five sleepers or more.
- Some counties outside
the UK adopt the post-tensioning method where tendons are placed in
debonding sheaths and the stress is applied after the concrete has
hardened by the application of tensile force to the tendons by
jacking and final anchoring. This method is slower but less capital
intensive and lends itself to small-scale production and situations
where demand is less.
- Standard prestressed
concrete sleepers used in the UK are normally 2515mm long by 264mm
wide. The depth varies from 203mm at the rail seat to 165mm at the
centerline giving a total weight of 285 kg.
- The prestress is
provided by six No. 9.3mm strands for standard use increased to
eight and strands for heavy-duty.
- These sleepers are
capable of sustaining an equivalent dynamic load of 24 tonnes at
each rail seat. Allowing for impact, lurching, wheel flats, poor
rail joints and etc this is equivalent to the effects of the
passage of a static 25 tonnes axle.
- Metros and light rail
systems have extensively also adopted prestressed concrete
sleepers. Where maximum axle loads are less than for mainline, the
sleeper dimensions may be reduced accordingly. However, great care
must be taken in the design to ensure that adequate allowance is
made for dynamic effects, particularly for bending
moments.
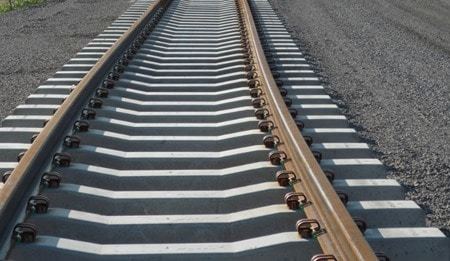
Twin-bloc concrete
sleeper
- The twin block
sleeper consists of two reinforced concrete blocks joined together
with a steel tie bar cast into the blocks.
- They are for
ballastless slab track, related to a railway sleeper of the type to
be used in particular for ballastless track or (concrete) slab
track and comprising two concrete blocks joined by a reinforcing
steel frame, said blocks being provided with holes intended to
house a fastening to secure a rail, preferably four holes which
allow the sleeper to be used for two different track gauges, thus
being multipurpose, and in any case with the particularity that
said sleeper blocks have an improved structural configuration which
provides significant advantages, both in their manufacturing and in
their effectiveness for absorbing displacements and loads of the
fastenings which support the rails, with respect to the systems
currently known for such purpose.
- This type of
sleeper is used extensively in Europe, particularly in France, but
not in the UK.
- The standard
sleeper weighs 230 kg which is less than the monobloc
equivalent.
- However, handling
and placing can be difficult due to the tendency to twist when
lifted.
- Twin block
sleepers can be provided with resilient 'boots' and can be
incorporated into non-ballasted slab track or monolithic embedment
in road surfaces for light rail street running.

Slab track
- Slab track, also called the
ballastless track, is a modern form of track construction which has
been used successfully throughout the world for high-speed lines,
heavy rail, light rail and tram systems.
- For this, first, we have to know
what is a ballasted track -
On the ballasted
track, the rail is mounted onto a wooden or concrete sleeper. The
sleeper sits on a bed of ballast (crushed rock) which distributes
the loading to the subgrade. “Top” ballast is placed between the
sleepers and on the shoulders to provide longitudinal and lateral
stability.
- Now, the slab
track is a type of railway track infrastructure in which the
traditional elastic combination of ties/sleepers and ballast is
replaced by a rigid construction of concrete or asphalt.
- In ballastless
tracks, the rails are rigidly fastened to special types of concrete
ties/sleepers that are themselves set in concrete. Ballastless
tracks, therefore, offer a high consistency in track geometry,
adjusting of which is not possible after the concreting of the
superstructure.

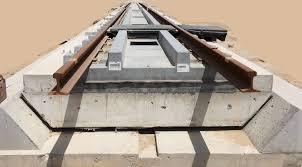
Concrete Slab
Track
-
With concrete track slab systems, the ballast is replaced by a
rigid concrete track slab which transfers the load and provides
track stability. Resilience is introduced into the track system by
means of elastomeric components. These may be pads, bearings, or
springs depending on the type of slab track system.
There are broadly
five types of a generic slab track system:
- Embedded rail
- Booted sleepers
- Direct fixing and resilient baseplates
- Cast-in sleepers
- Floating slab
Within each generic group, there are a
large number of variants and proprietary systems available. Slab
track can be designed and optimized to suit the required
application.
Advantages of slab track
Slab track offers the following
advantages over the traditional ballasted track:
- Very low maintenance requirements
- Shallow construction depth
- Reduced dead load
- Reduced structure gauge
- Higher speed operation
- Engineered noise and vibration performance
- Long design life
- Increased reliability
- Increased availability
- Low whole-life cost
- A sustainable solution
Disadvantages of slab track
- Higher cost of initial
construction.
While numbers vary depending on
construction type and track infrastructure (ballastless tracks are
generally more suitable to infrastructures that are also made of
concrete, as is the case in tunnels or on viaducts)
It is estimated in 2015 that
construction costs of ballastless tracks are 40 percent higher than
those of traditional superstructure. However, the life-cycle cost
of ballastless tracks is generally lower than those of ballasted
tracks due to significantly lower maintenance.
- impossibility of adjusting or
correcting track geometry once the concrete has been set
- the necessity of a stable
infrastructure (since no adjustments can be made to the
superstructure)
- higher noise emissions
- longer repair times when the concrete
slab is damaged (e.g. due to construction faults or wear and
tear).